Common Costly Mistakes in Heavy-duty Truck Repairs and How To Avoid Them
Discover common pitfalls in heavy-duty truck repairs and how to avoid costly mistakes. Learn about best practices to prevent repeat failures and reduce downtime efficiently.
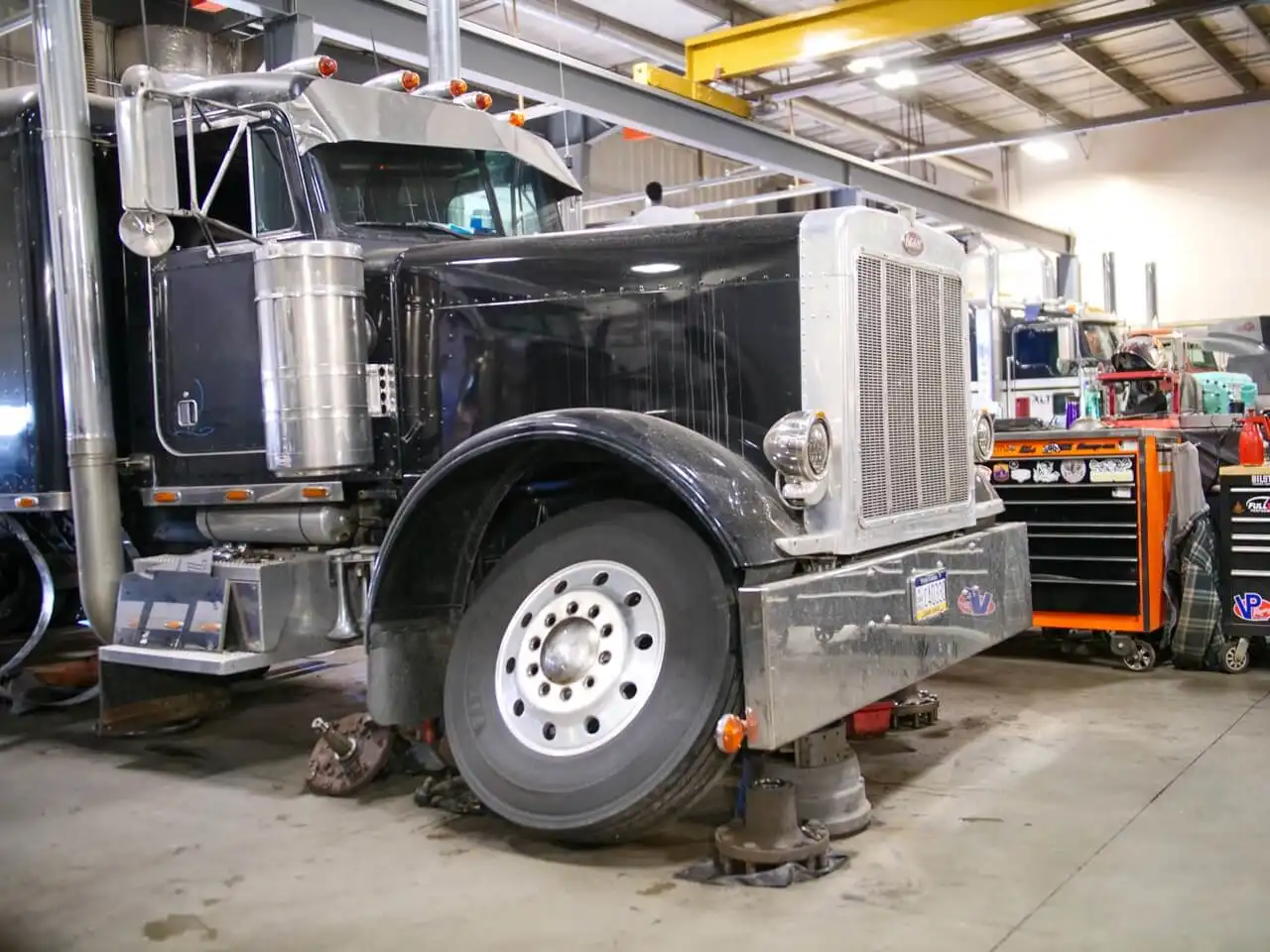
Heavy-duty truck repairs can be complex and expensive undertakings. Even small oversights or missteps during diagnostics, disassembly or reassembly can lead to repeat failures and extended downtime. Being aware of common pitfalls in truck repair can help technicians avoid making expensive mistakes. Here are some frequent oversights and tips to prevent them:
Not Identifying the True Root Cause
A common mistake is only fixing the obvious symptom rather than properly diagnosing and identifying the failure's root cause. For example, simply replacing a failed part without determining what underlying issue led to the failure in the first place. Proper diagnosis requires thoroughly troubleshooting issues, inspecting components, and testing systems to trace problems back to their origin before taking repair action. Making assumptions or taking shortcuts leads to repeat failures.
Using Cheap Aftermarket Parts
While less expensive upfront, low-quality aftermarket or remanufactured components often fail sooner than quality OEM or equivalent parts. The minor savings from installing a cheap part can quickly be erased by another repair or roadside breakdown caused by early failure of the inferior part. It pays to use trusted brands and parts with robust warranties.
Neglecting Supporting Systems
When replacing major components like engines, transmissions, or drive axles, technicians sometimes narrowly focus on the main assembly and overlook supporting systems that connect to it. Critical items like mounts, connectors, seals, wiring harnesses, sensors, cooling lines, and fasteners need to be carefully inspected when doing major component R&R. Worn items should be replaced to avoid secondary failures of the newly installed component.
Not Following Proper Re-Torque Procedures
Many critical parts and fasteners are initially installed with torque-to-yield bolts that are meant to stretch upon the first torquing sequence. It is imperative to follow the manufacturer's re-torque procedure after a short test drive or run time to ensure these types of bolts maintain proper clamping force. Neglecting this can lead to lost parts and failures.
Reusing Old Parts
Some technicians, in an effort to save time or money, reuse U-joints, gaskets, seals, O-rings, bearings, and other hardware when reassembling components or making repairs. However, manufacturers intend these items to be used once and then replaced. Attempting to reuse old pieces often leads to leaks, premature wear, and failures shortly after reassembly. Always install new hardware.
Cutting Costs On Fluids
Using lower quality or insufficient fluids during repairs can negatively impact lubrication, cooling, component wear and overall performance. Whether engine oil, transmission fluid, coolant, or grease, always refill assemblies with the manufacturer's recommended fluid type and quantity after repairs. Don't try to save money on fluids.
Improper Assembly
Reassembling components incorrectly can potentially cause binding, accelerated wear, fluid leaks, and early failures. When reassembling parts, carefully follow OEM torque patterns, tightening sequences, and gasket positioning. Double-check your work and confirm that everything is lined up and moving freely before completing it.
Rushing Through the Job
Moving too quickly during disassembly, repair work and reassembly can lead technicians to overlook critical steps, improper torquing, the introduction of contaminants/debris into assemblies, and not properly setting components back to specifications. Allow adequate time in schedules to fully complete repairs correctly the first time without rushing.
Skipping Post-Repair Road Testing
It's critical to thoroughly road test repairs over varying operating conditions before releasing a truck back into service. On-road testing often catches issues missed in the shop, like fluid leaks, vibrations, pulling, noises, loose parts, and diagnostic faults. Don't skip this final step.
Not Thoroughly Cleaning Surfaces
Failing to completely clean mounting surfaces when removing parts, like gearboxes or engines, can allow old debris, contaminated oil, and gasket material to enter the assembly upon reinstallation. This debris causes premature wear and damage. Carefully scrape and clean all surfaces prior to reassembly.
Additional Tips
- Not Following Torque Procedures: Neglecting to torque critical fasteners and hardware to OEM specs can lead to lost parts, leaks, and potential failures. Always use a properly calibrated torque wrench.
- Damaging Fastener Heads: Using improper tools can damage fastener heads, which then requires drilling out and re-tapping holes. Use the correct sized, quality tools.
- Replacing Only One Worn Part: If one part shows wear, chances are related components are also worn. Replace all worn pieces together to avoid another failure.
- Not Testing Repairs Under Load: Test repaired equipment like a dyno test engine. Load testing checks operations and identifies problems before returning to service.
- Incorrect Fastener Grade: Bolt grades have specific torque values and uses. Always replace with the same grade or better fasteners.
- Allowing Contaminants Inside: Not covering exposed components during repair allows dirt, debris, and moisture contamination. Tape or cap all openings.
- Incorrect Alignment: Reinstalling components that are slightly misaligned puts stress on systems. Precision alignment is critical.
- Not Confirming Repair: Assuming a repair fixed the problem without testing leads to repeating repairs. Verify operation before release.
- Improper Gasket Seating: Not properly seating gaskets during installation causes leaks. Ensure proper contact and consistent pressure.
Conclusion
Avoiding common oversights and mistakes takes diligence and care during heavy truck repairs but saves significantly on costs and downtime in the long run. Following repair best practices ensures work is done correctly the first time.
For more information on our diesel truck repairs and services, click here!
More Articles
.webp)
What to Look For in Professional Heavy-Duty Preventive Maintenance

How Preventive Maintenance Saves You Money
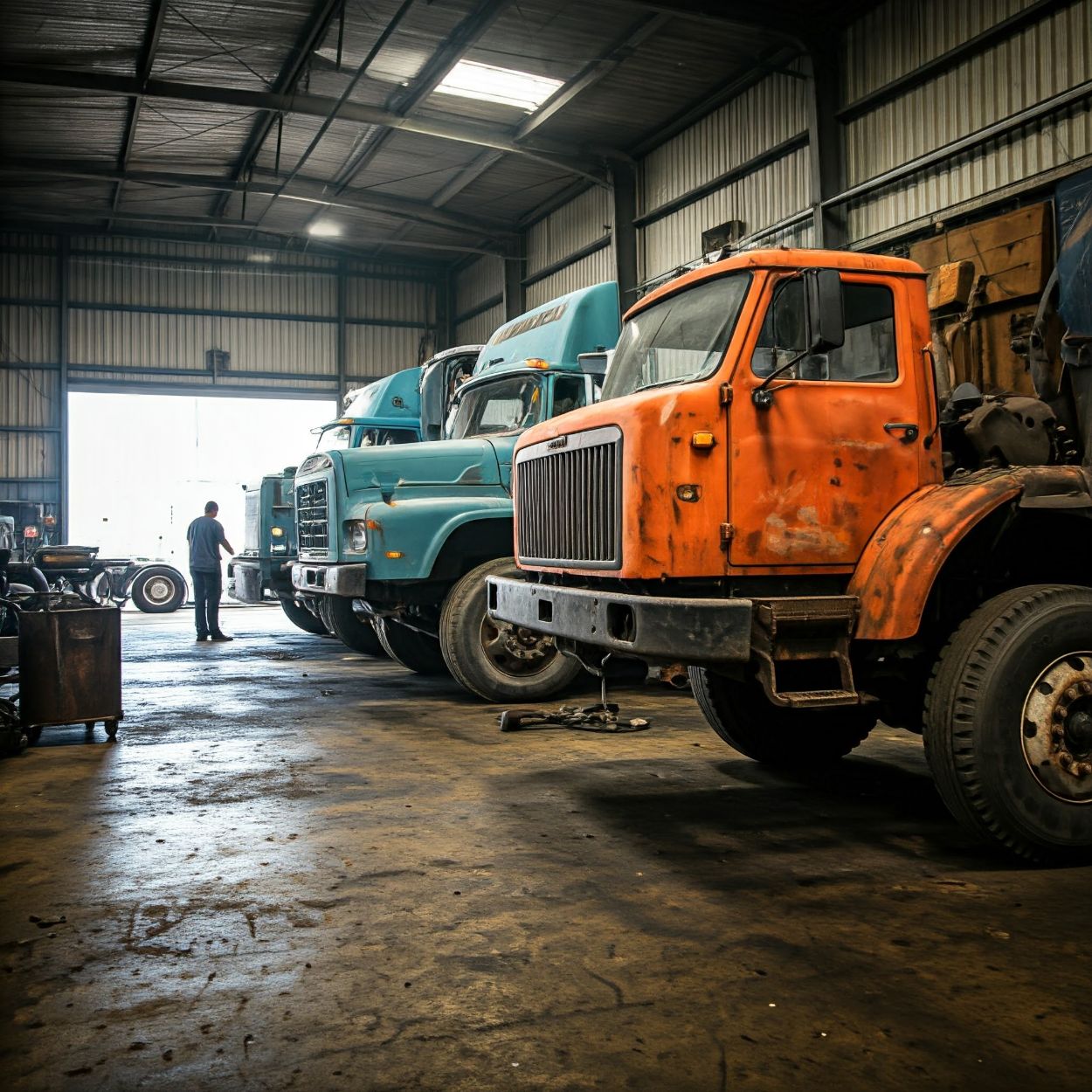
What Maintenance Does Your Fleet Need This Winter?
Contact Us
Get in touch with TCB Truck Service today to schedule service in-shop in Memphis, Tennessee, or via mobile service within 150 miles, including service to northern Mississippi & eastern Arkansas.
We're open Monday through Friday, from 7:00am to 4:00pm.